9 Best Practices for Setting up your Ecommerce Warehouse
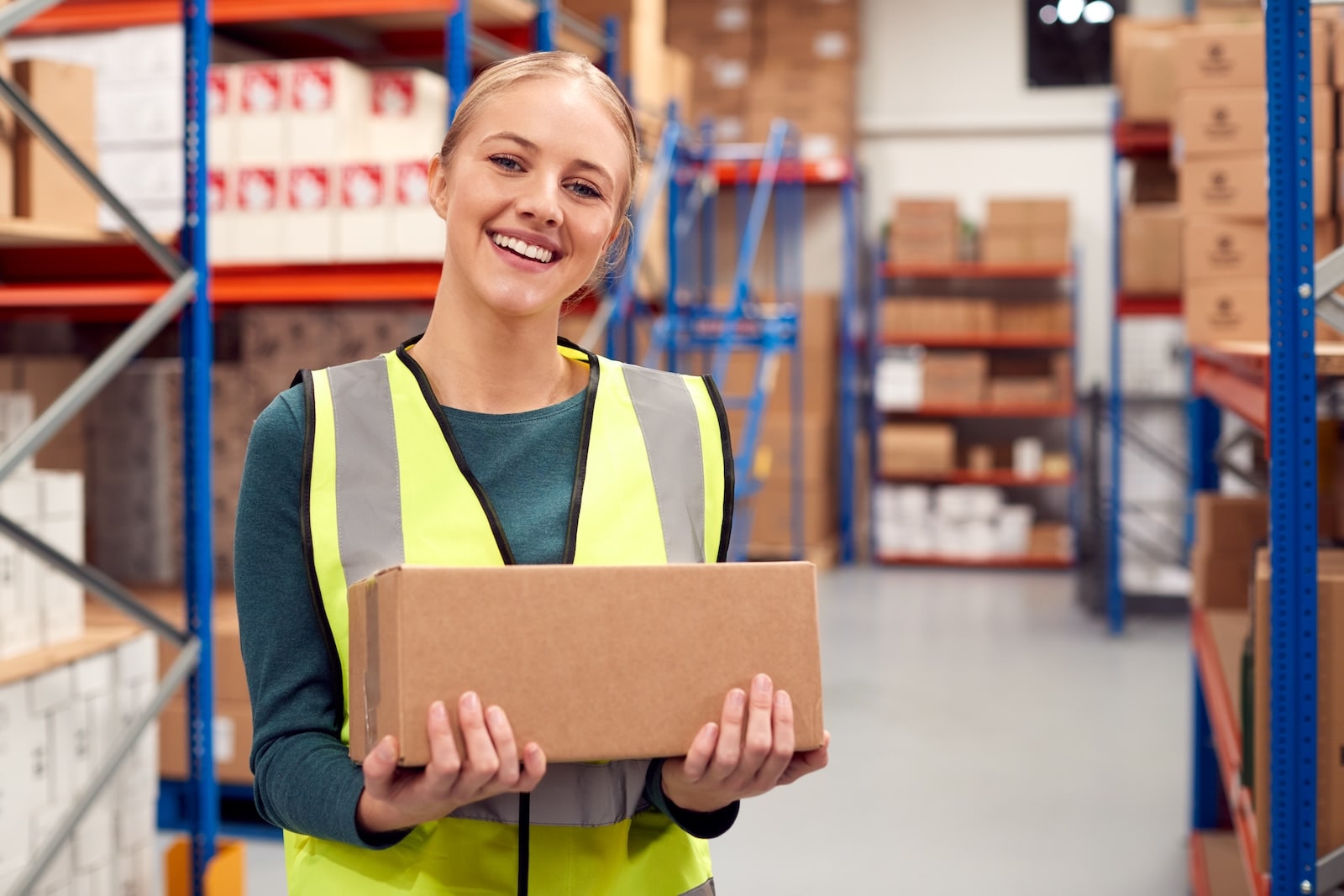
When you’re running an ecommerce business, having efficient warehouse management is essential for your success. A well-organised warehouse not only boosts productivity but also ensures timely deliveries and satisfied customers.
When you’re running an ecommerce business, having efficient warehouse management is essential for your success. A well-organised warehouse not only boosts productivity but also ensures timely deliveries and satisfied customers.
In this post, we’re sharing our best practices for setting up your e-commerce warehouse. Follow this guide to optimise operations and create a productive environment for your business.
1. Choose the Right Location
The location of your warehouse is a critical factor. It should be strategically placed to minimise shipping times and costs. Consider proximity to major highways, ports, and your primary customer base. A centrally located warehouse can reduce transit times and shipping costs, ensuring faster delivery to customers.
2. Optimise Warehouse Layout
An efficient warehouse layout can significantly enhance productivity. The design should facilitate a smooth flow of goods from receiving to shipping.
Divide your warehouse into zones such as receiving, storage, picking, packing, and shipping. This separation helps streamline processes and reduces the likelihood of errors.
Ensure that aisles are wide enough for equipment and staff to move freely. This reduces congestion and increases safety.
Make the most of your vertical space through installing shelving and racking systems. On your floor space, use high-density storage solutions to maximise efficiency.
3. Implement a Warehouse Management System
A Warehouse Management System (WMS) is essential for efficient warehouse operations. It helps in tracking inventory levels, managing stock locations, and processing orders.
WMS enables real-time tracking of inventory levels, reduces errors and prevents stockouts or overstocking. It also automates repetitive tasks and streamlines processes such as picking, packing, and shipping. Plus, it provides valuable insights into warehouse operations, helping in making informed decisions.
Streamline Receiving and Inspection
Efficient receiving and inspection processes are crucial for maintaining inventory accuracy and quality control. Best practices include:
- Standard Operating Procedures (SOPs): Establish clear SOPs for receiving and inspecting goods. This ensures consistency and reduces errors.
- Inspection Area: Designate a specific area for inspecting incoming goods to prevent contamination or damage to existing inventory.
- Documentation: Ensure all received goods are properly documented and discrepancies are promptly reported.
4. Ensure Efficient Picking and Packing Processes
If you’re running a fresh produce business, then you’ll know how time consuming picking and packing can be. They are labour-intensive processes that directly impact the speed at which you can fulfil orders. To make things faster, try these strategies.
- Order Picking Strategies: Use appropriate picking strategies such as batch picking, zone picking, or wave picking based on order volume and warehouse layout.
- Packing Stations: Set up ergonomic packing stations with all necessary supplies within reach. This reduces time spent on each order and improves efficiency.
- Quality Control: Implement a quality control process to check orders before shipping. This reduces the likelihood of returns and increases customer satisfaction.
5. Effectively Manage your Inventory
Effective inventory management ensures that you have the right products in the right quantities at the right time. If you’re finding it difficult to keep track of your inventory, try these techniques.
- ABC Analysis: Categorise inventory into three groups (A, B, C) based on value and turnover rate. This helps prioritise high-value and fast-moving items.
- Safety Stock: Maintain a buffer stock of high-demand items to prevent stockouts during peak seasons or supply chain disruptions.
- Cycle Counting: Regularly count a portion of your inventory to ensure accuracy and identify discrepancies.
6. Leverage Technology
Technology can significantly enhance warehouse operations. Invest in the following technologies:
- Barcode Scanners and RFID: These tools improve accuracy in inventory tracking and reduce manual entry errors.
- Automated Guided Vehicles (AGVs): AGVs can transport goods within the warehouse, reducing labour costs and increasing efficiency.
- Warehouse Robots: Robots can assist in picking and packing processes, further boosting productivity and accuracy.
7. Ensure Safety and Compliance
Safety should be a top priority in your warehouse. Make sure to provide regular safety training for all employees. Ensure they are aware of proper lifting techniques and equipment operation.
Then, consider your machinery and equipment. Remember to equip your warehouse with safety gear such as helmets, gloves, and high-visibility vests. Ensure that all equipment is regularly inspected and maintained.
It’s also important to establish clear emergency procedures and conduct regular drills to ensure your team is prepared.
8. Create a Comfortable Space for Your Team
A comfortable and positive work environment is crucial for employee satisfaction and productivity. Consider the following:
- Ergonomic Workstations: Ensure that workstations are designed ergonomically to reduce physical strain and prevent injuries.
- Break Areas: Provide clean and comfortable break areas where employees can relax and recharge during their breaks.
- Climate Control: Maintain a consistent and comfortable temperature within the warehouse to prevent discomfort during extreme weather conditions. For example, you can install warehouse fans to improve airflow and keep your staff cool.
- Positive Work Culture: Foster a positive work culture by recognising employee achievements, encouraging open communication, and providing opportunities for growth and development.
9. Enable Continuous Improvement
The ecommerce landscape is constantly evolving, and your warehouse operations should adapt accordingly. Embrace a culture of continuous improvement by conducting regular audits of your warehouse processes to identify areas for improvement.
Encourage employees to provide feedback on warehouse operations. They can offer valuable insights into potential inefficiencies.
Keep updated on industry trends and advancements in warehouse management technologies. Implement new practices and tools that can enhance efficiency.
Final Thoughts
Setting up an efficient ecommerce warehouse requires careful planning and execution. Through following these tips, you can ensure your warehouse is a space where your team can thrive and your business can achieve its goals.